Rental & Service
Comparing the pros and cons of renting vs. buying
Subject | Renting | Buying |
---|---|---|
Budget savings and manageability |
|
|
the need for professional technicians |
|
|
Securing spare parts and consumables |
|
|
Training |
|
|
Induction Bolt Heating Services
The safest and most efficient technology for turbine bolts.
Our induction bolt heaters are designed to improve difficult and dangerous conventional electric bolt heater environments, preventing heavy and dangerous hammering bolting, and dramatically reducing the risk of burn injuries and bolt damage seen in conventional methods.
Induction heating technology is very state-of-the-art, highly efficient, and safe. We sell induction bolt heaters and provide on-site bolt heating services. We also provide training programs for personnel in charge of operating equipment.
Increase the productivity of plant maintenance with fast, easy, accurate, and repeatable high-efficiency heat transfer technology. Induction bolt heating is up to four times faster and up to three times lower in temperature than conventional electrical resistance bolt heater methods. You can move freely anywhere in the workplace or in the field, change the one-touch quick joint inductor coil in seconds, and use the flexible coil can be flexibly bent over in very narrow and obstructed environments. The nut heating coil is the best way to break down rust or stuck bolts. It’s very simple and easy to use, so anyone can learn quickly.
- It is a mobility design that allows flexible connection of power output cables up to 20 meters or more.
- Various coils can be installed to fit bolt dimensions of all sizes.
- Provides a high-efficiency nut heating coil for resolving rust and stuck bolt issues.
- The flexible coil can be flexibly bent over in very narrow and obstructed environments.
Nuclear Power |
|
![]() |
---|---|---|
Thermal Power |
|
![]() |
Hydro-Electric Power |
|
![]() |
Petrochemical |
|
![]() |
Paper Manufacturers |
|
![]() |
Steel Manufacturers |
|
![]() |
Model | HeatBolt 30 | ![]() |
![]() |
---|---|---|---|
Body Type: | Chiller Integrated System | ||
Max. Output Power: | 30KW | ||
Frequency Range: | 1~ 100kHz | ||
Output Power Regulation Range: | 2~100% | ||
Power Supply Efficiency: | ≥95% | Power Supply | Power Supply |
Induction Shrink Fitting Services
In the case of the conventional resistance heating method, if the electric heater is installed in the retaining ring during shrink fitting, the heater is wound and covered with asbestos to prevent heat loss at this time, fine asbestos powder is generated, which is a risk to the operator, and there is a risk of burns to the operator due to the high temperature of the coil. In addition, heat can be conducted to the shaft and is time consuming because it must be heated for 90 to 120 minutes with a 200kW electric resistance heater. Since there are problems in terms of long heating time and worker safety, it improves the quality of work while solving these problems. To ensure the same quality of work, our induction heating system has improved workability and safety by addressing existing difficulties.
![]() |
![]() |
Electric Resistance Heater | Induction Shrink Fitting |
Outside Diameter (O.D.) | 1200mm | ![]() |
---|---|---|
Total Heated Length | 890mm | |
Thickness | 76mm | |
Weightof Retaining Ring | 230Kg±10% | |
Max. Heating Temp | 350°C | |
Elongation | 5mm |
Model | HeatFit 100 | ![]() |
![]() |
---|---|---|---|
Body Type : | External Chiller System | ||
Max. Output Power : | 100KW | ||
Frequency Range : | 1~ 100kHz | ||
Output Power Regulation Range : | 2~100% | ||
Power Supply Efficiency : | ≥95% | Power Supply | External Chiller System |
Induction Brazing Services
Induction Brazing Quality Management Response-Alloy does not penetrate the gap in the base material sufficiently. In the presence of a void in the brazing part, it combines with the alloy component to promote corrosion progress. Our company uses a high-frequency induction heating method that controls the base material at a uniform heating temperature. It has improved quality compared to the existing gas torch work method. To ensure perfect penetration of the filler material (alloy) into the gap of the base material, designed/manufactured by optimizing the shape of the work coil.
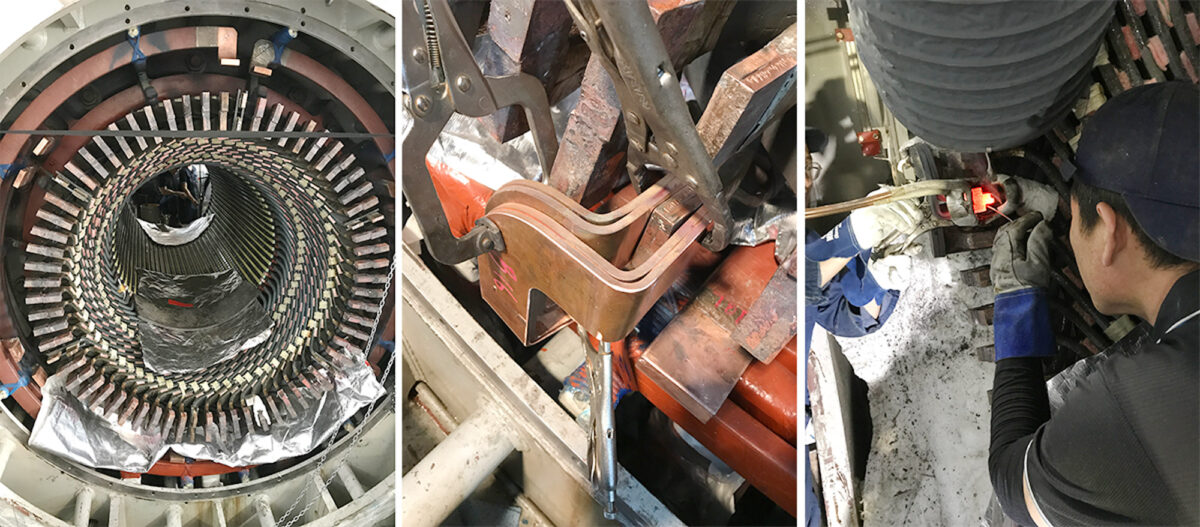
Model | HeatBrazing 100 | ![]() |
![]() |
---|---|---|---|
Body Type: | External Chiller System | ||
Max. Output Power: | 100KW | ||
Frequency Range: | 1~ 100kHz | ||
Output Power Regulation Range: | 2~100% | ||
Power Supply Efficiency: | ≥95% | Power Supply | Portable Current Transfer |
Consulting in Induction Heating Technology
We find the right heating solution to improve our customers’ productivity and ensure that they do the right thing through technical consulting. You will learn where and how to gain the benefits of induction heating in manufacturing or mobility applications. We can also support you through computer simulations, implementation plans, and return on investment calculations. If you already have an induction heating solution, look at how to improve the process and support your staff.
- Coil Design
- Cooling Systems
- Current Transformer
- PLC Panel
- HMI Design
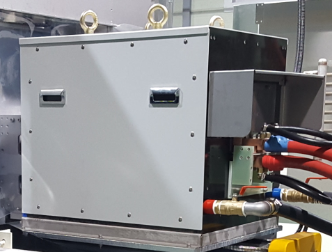
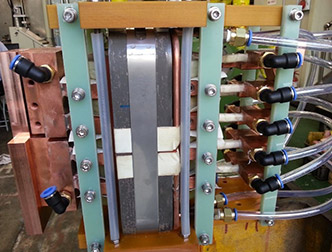
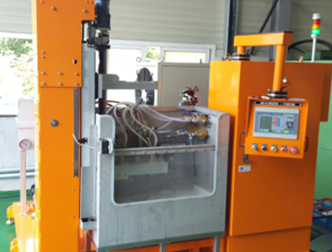
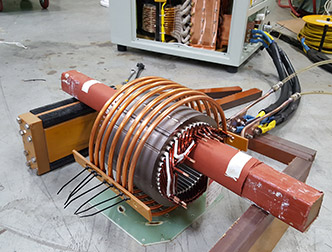
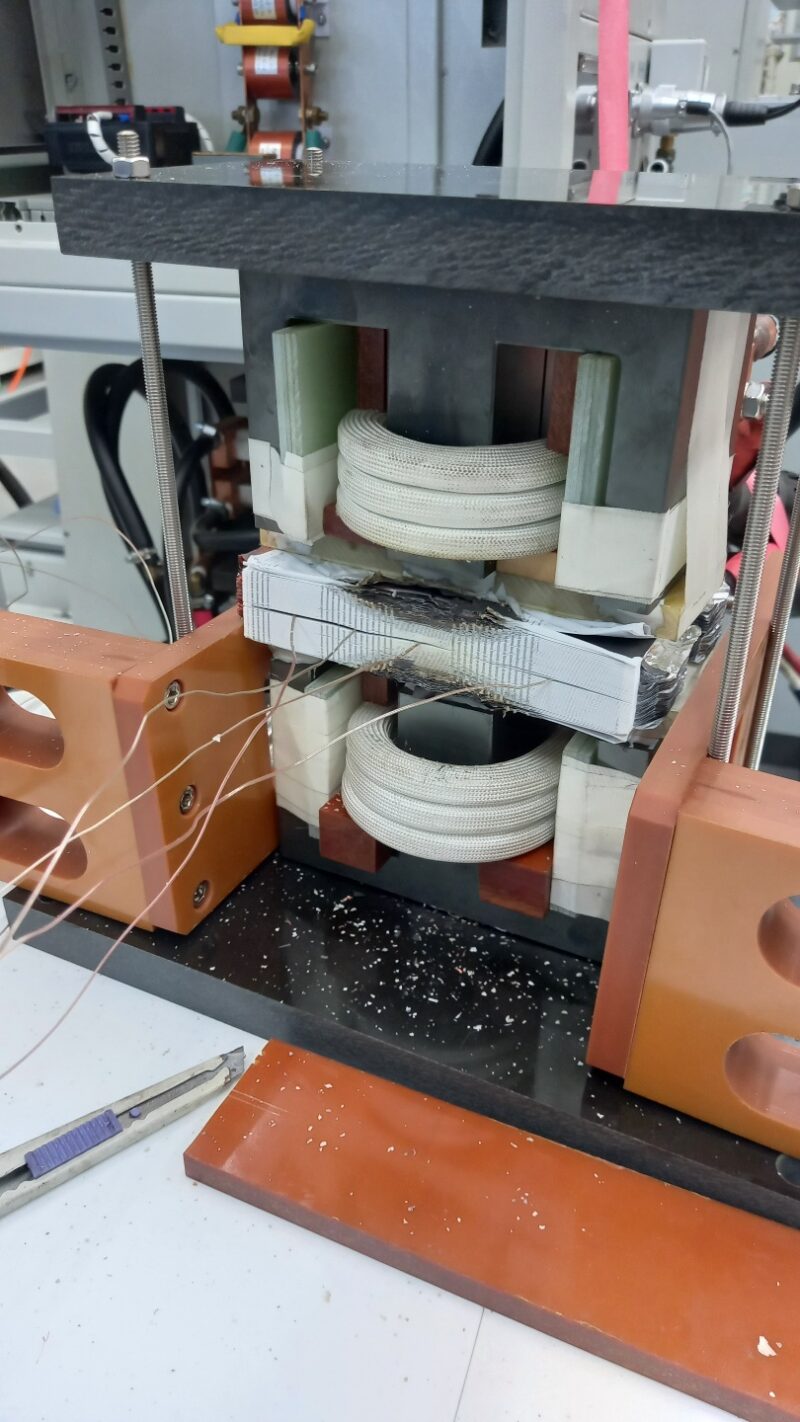
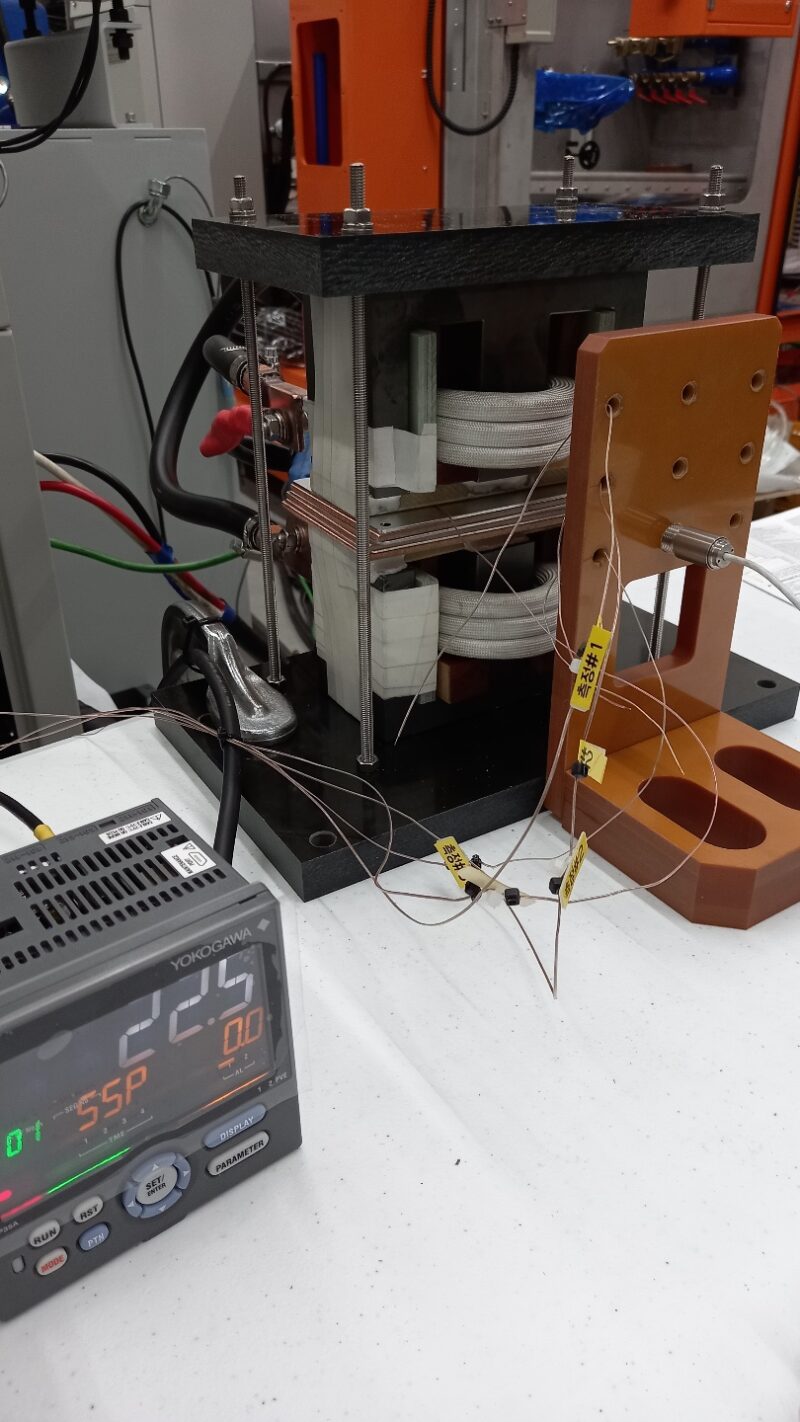
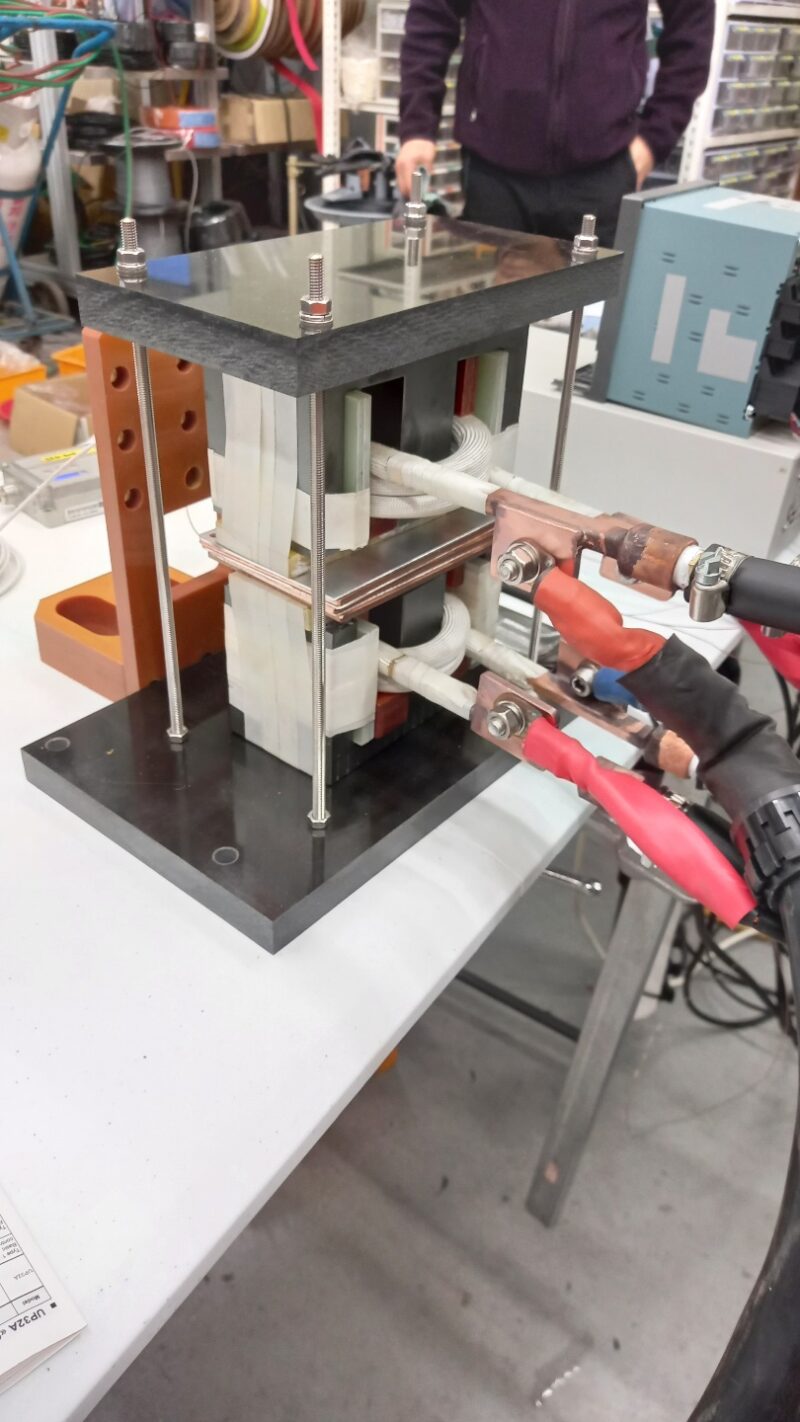
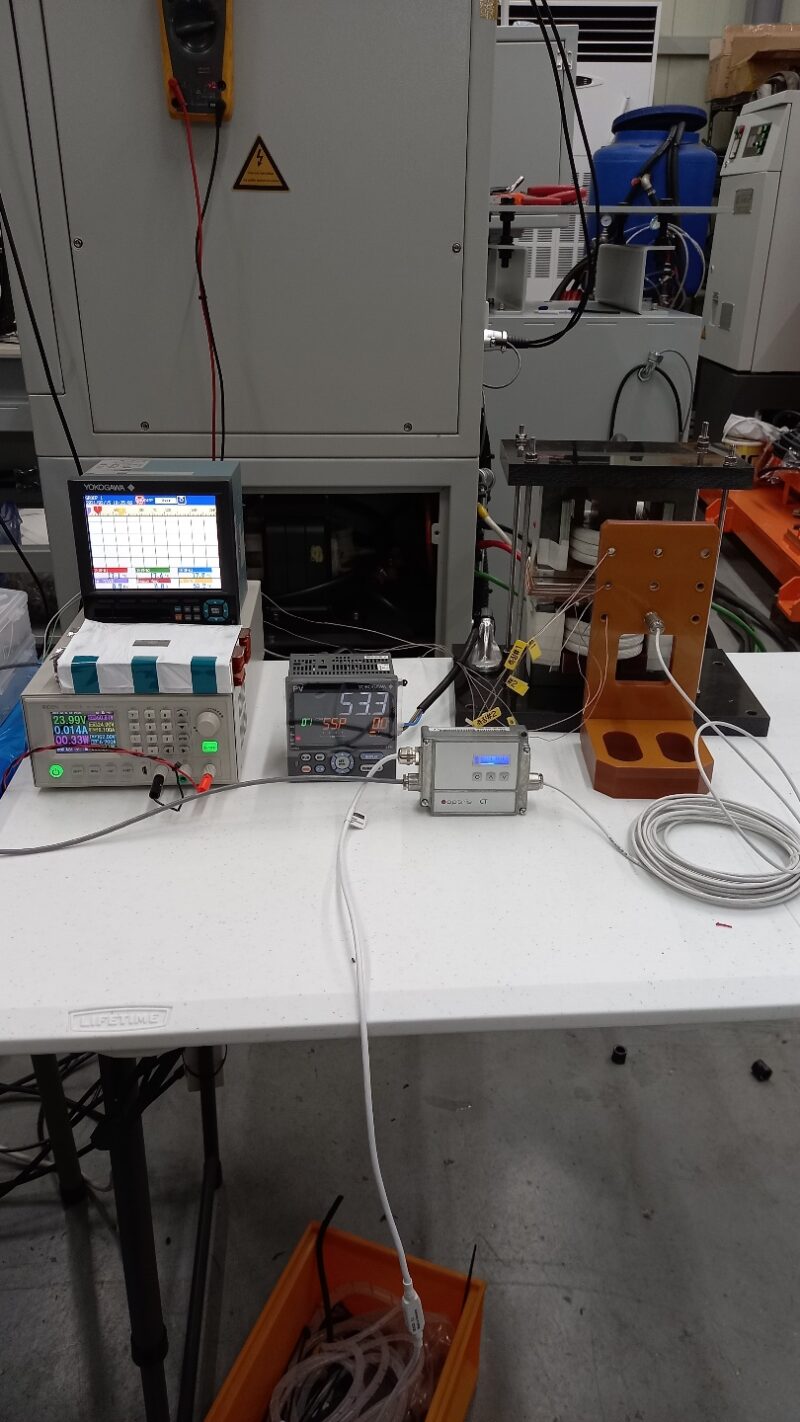